Covestro AG
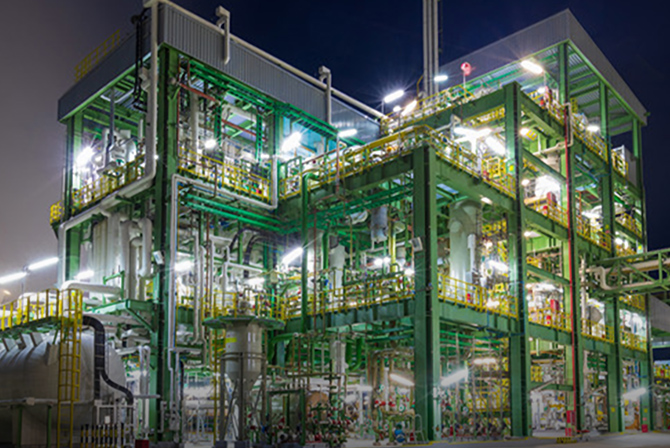
“From HCl By-Products
to Functional Materials and Circularity Using
the Highly Efficient HCl Oxidation Process
from Licensor Sumitomo”
Before
Internal recycling of Hydrogen Chloride from isocyanate production limited to electrolysis technologies with large scope 2 CO2 emissions
After
A reliable new technology option that supports Covestro’s strategic goals of reducing scope 2 CO2 emissions and pushing circular economy.
What made you select Sumitomo*s HCl Oxidation License?
“Covestro is a global producer of advanced materials with applications in automotive and transportation, construction, wood and furniture, electrics and electronics. Amongst COV’s products are isocyanates, that are needed as building blocks for polyurethanes. In isocyanate production Chlorine (Cl2) facilitates the amine to isocyanate reaction (addition of the carbonyl group), thereby Hydrogen Chloride (HCl) is formed as a stoichiometric by-product. At our integrated site Caojing the HCl demand of our customers is lower than our HCl production. Hence recycling of gaseous HCl into Cl2 is a preferred pathway (closing the Cl2 loop). The HCl Oxidation technology enables this pathway with a very low specific CO2 footprint.”
How did Sumitomo HCl Oxidation License help Covestro?
“At the integrated site Caojing the HCl Oxidation process (Deacon) turned out to be the perfect match for our twin needs of reducing energy demand and fostering circularity. After acquiring the process license from Sumitomo, we started the construction of “Deacon I”, our first industrial scale HCl Oxidation plant in 2008, and it was put into operation in 2011. At the end of 2018, “Deacon II” broke ground as a “smart copy” – the two Deacon plants leveraging very similar unit operations, operational procedures and equipment, thus resulting in synergies for plant operators. Sumitomo was a very valuable licensor and partner during planning, construction and start-up of the plant.“
With Sumitomo’s HCl Oxidation process, 98% of the hydrogen chlorine generated during the production of isocyanates is recycled at our Shanghai site. As a result, the corresponding CO2 emissions fall from over 150,000 to just over 9,000 metric tons per year compared to the salt electrolysis, an extraordinary reduction of about 94%. Part of the savings is coming from the heat generated during the process being fed back into the production cycle in the form of steam. And in recognition of our continuous efforts in using innovative processes that ensure greater sustainability in manufacturing, our Shanghai site was in 2018 granted the National Green Factory certificate by the Ministry of Industry and Information Technology, becoming the first of its kind inside the Shanghai Chemical Industry Park to obtain this kind of prestigious recognition”.
What is Covestro’s future outlook?
“Covestro’s scope 1&2 climate neutrality target by 2035 and our circularity aspiration are guiding principles for the transformation of our production sites worldwide. The HCl Oxidation process as licensed by Sumitomo is a very valuable technology to recycle gaseous HCl from isocyanate production to Cl2 with very low CO2 footprint, achieving required Cl2 specification, and high reliability. We are eager to continue our strong collaboration with our valued licensor and partner Sumitomo”
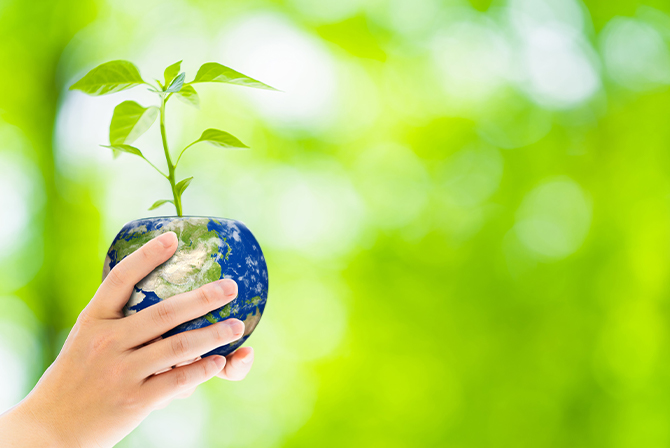
Remarks by Sumitomo Chemical
This success story is a typical example on how our highly innovative process was utilized by a very valuable licensee to contribute to circular economy, going hand in hand with a significant reduction of energy consumption and carbon footprints. It further highlights the environmentally friendly nature of our technology when using gaseous hydrogen chloride. Finally, Covestro’s success story further demonstrates the broad applicability of our innovative process in the overall optimization of the chlorine value chain and achievement of sustainable production.