- 製品情報
- スミカエクセル PES
- パウダー用途
スミカエクセル PESのパウダー用途
スミカエクセルPESのパウダーの特徴
スミカエクセルPESのパウダーグレードは以下の用途に好適です。
- 溶媒に溶解させて接着剤、塗料・コート剤として使用
- 溶媒に溶解させて中空糸膜やキャスト膜(平膜)に加工
- スミカエクセルPESベースの各種コンパウンド用途やエポキシ強化用途
パウダーグレードとして次のグレードを取り揃えています。
表7-1 スミカエクセルPESパウダーグレード
パウダーグレード | RV(還元粘度)* | 主用途 |
---|---|---|
3600P | 0.36 | コンパウンド |
4100P | 0.41 | 塗料・コート剤、接着剤 |
4800P | 0.48 | 中空糸膜、接着剤 |
5003PS | 0.50 | 塗料・コート剤、接着剤、エポキシ強化剤 |
5200P | 0.52 | 中空糸膜 |
5900P | 0.59 | 中空糸膜 |
7600P | 0.76 | 中空糸膜 |
* 還元粘度は、ジメチルホルムアミド(DMF)1%溶液中で測定したものです。
表7-2 スミカエクセルPESのグレードラインナップ
還元粘度 | 0.36 | 0.41 | 0.48 | 0.52 | 0.59 | 0.76 | ||
---|---|---|---|---|---|---|---|---|
パウダー | 3600P | 4100P | 4800P | 5200P | 5900P | 7600P | ||
5003PS* | ||||||||
ペレット | 非強化 | 3600G | 4100G | 4800G | ||||
ガラス繊維強化 | 3601GL20 | 4101GL20 | ||||||
3601GL30 | 4101GL30 |
* 末端OH含有グレード
スミカエクセル パウダーグレードの物性
スミカエクセル3600P、4100P、4800Pの性質
パウダータイプの3600P、4100P、4800Pの物性値は、ペレットタイプの3600G、4100G、4800Gの物性値と同等です。
表7-3 3600G、4100G、4800Gの物性値
テスト方法 | 単位 | 3600G/4100G/4800G | ||
---|---|---|---|---|
一般的物性 | 密度 | ISO 1183 | g/cm3 | 1.37 |
成形収縮率(MD) | 住化法 | % | 0.60 | |
成形収縮率(TD) | 住化法 | % | 0.60 | |
吸水率(23℃、24hr) | ISO 62 | % | 1.0 | |
機械的性質 | 引張強度 | ISO 527-1,2 | MPa | 85 |
引張降伏ひずみ | ISO 527-1,2 | % | 6.5 | |
曲げ強度 | ISO 178 | MPa | 130 | |
曲げ弾性率 | ISO 178 | MPa | 2,600 | |
アイゾット衝撃強さ(ノッチなし) | ISO 180/1U | kJ/m2 | 破壊しない | |
アイゾット衝撃強さ(ノッチ付き) | ISO 180/1A | kJ/m2 | 8 | |
ロックウエル硬さ(Mスケール) | ISO 2039-2 | - | 95 | |
熱的性質 | 荷重たわみ温度(0.45MPa) | ISO 75 | ℃ | 214 |
荷重たわみ温度(1.80MPa) | ISO 75 | ℃ | 205 | |
線膨張係数(MD) | ISO 11359-1,2 | 10-5/K | 5.5 | |
線膨張係数(TD) | ISO 11359-1,2 | 10-5/K | 5.5 | |
電気的性質 | 比誘電率(絶乾:100Hz) | IEC 62631-2-1 | - | 3.5 |
比誘電率(絶乾:1MHz) | IEC 62631-2-1 | - | 3.4 | |
比誘電率(絶乾:1GHz) | IEC 60250 | - | 3.4 | |
誘電正接(絶乾:100Hz) | IEC 62631-2-1 | - | 0.002 | |
誘電正接(絶乾:1MHz) | IEC 62631-2-1 | - | 0.004 | |
誘電正接(絶乾:1GHz) | IEC 60250 | - | 0.004 | |
体積抵抗率 | IEC 62631-3-1 | Ω・m | >1013 | |
絶縁破壊強さ(1mm) | IEC 60243-1 | kV/mm | 43 | |
耐トラッキング性 | IEC 60112 | V | 150 | |
燃焼性 | 難燃性分類 | IEC 60695-11-10 | - | V-O |
限界酸素指数(1.6mm) | ASTM D2863 | % | 38 |
スミカエクセル5003P、5003PSの性質
- ガラス転移点、230℃を有する非晶性樹脂です。
- 100重合繰り返し単位当たり、0.6~1.4と多くの末端水酸基を有しているために接着性が良好です。
- 他の性質はスミカエクセルPESの他のグレードと同等です。
塗料・コート分野
塗料・コート分野にはスミカエクセル4100P、5003PSが使用されています。特に、5003PSは熱時硬度、耐薬品性と金属との接着力を強化したグレードです。
スミカエクセル5003PSを使用した塗料・コート剤について述べます。
スミカエクセル5003PS使用塗料・コート剤の特徴
- 空気中で250℃の長期使用、あるいは冷熱サイクル(0℃⇔250℃)使用に対しても安定です。
- 接着性、密着性=ガラス、セラミックス、鉄、ステンレス、アルミニウムあるいはアルミニウム合金等に対して優れた接着性を発揮します。
- 耐溶媒性=非晶性樹脂の中では優れた耐溶媒性を示します。
- 耐加水分解性=ポリエーテルサルホン樹脂自体、耐加水分解性に優れた樹脂であり、5003PSは更に優れた耐加水分解性を示します。
- 良成膜性=成膜性に優れ、基材を十分に保護します。
- 難燃性=難燃剤無添加で高い難燃性を有しております。
- 透明性=優れた透明性を有しており、コート後も基材のままの外観を保持します。
- 衛生性=可塑剤等の添加剤を含まず衛生的です。
スミカエクセル5003PSの塗布方法(溶液法の例)
- 基材を脱脂、必要に応じてブラストまたはエッチングを行う。
- スミカエクセル5003PSを溶媒に溶解させる。
- この溶液を浸漬、はけ塗り、スプレー法等で基材に塗布し、20分間風乾する。
- 350~400℃、空気中で30分間焼成処理を行う。
ゲル化防止
スミカエクセルPES溶液はゲル化する場合がありますが、PES分子と溶媒の双方が絡む結晶化と説明されています。
(特徴)
- 溶液が濁り、全体が固化する場合がある。
- ゲルが生成した場合、溶媒を加えても再溶解は困難。
- ゲルは未ゲル化溶液をゲル化させる核となる。
- 温度をかけることで融解して元の溶液に戻る。
(ゲル化防止)
- 過度のせん断応力を加えない。ホモジナイザーの使用は避けてください。
- 高濃度状態で長時間置かない。未撹拌の溶媒中に膨潤したPESを放置しないでください。
- 混合溶媒の使用を推奨します。
濃度-粘度相関性
スミカエクセル4100Pと5003PSのNMP溶液の濃度-粘度相関性は下記の通りです。
図7-1 スミカエクセル4100Pと5003PSのNMP溶液の濃度-粘度相関性
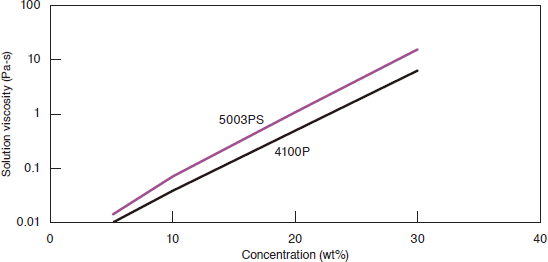
アルミニウム板におけるスミカエクセル5003PSコートの耐熱性(例)
表7-4 連続使用耐熱性(250℃空気中)
評価項目 | 時間(hr) | ||
---|---|---|---|
0 | 115 | 235 | |
外観変化 | - | 変化なし | 変化なし |
碁盤目試験*1 | 100/100 | 100/100 | 100/100 |
耐食テスト*2 | 腐食なし | 腐食なし | 腐食なし |
表7-5 冷熱サイクルテスト(0℃氷水中2分と250℃空気中2分のサイクル)
評価項目 | サイクル回数(回) | ||
---|---|---|---|
0 | 25 | 50 | |
外観変化 | - | ほとんど変化なし | エッジ部若干発泡 |
碁盤目試験*1 | 100/100 | 100/100 | 100/100 |
耐食テスト*2 | 腐食なし | 腐食なし | 腐食なし |
*1 スミカエクセル5003PSコート層を基材にいたるまで、安全かみそりで100mm2の面積にわたり1mm×1mmの交差碁盤目状に刻みを入れ、次いでセロハン粘着テープを押しつけて押圧後、剥離して、基材に残ったスミカエクセルPES切片の個数。
*2 スミカエクセル5003PSコート面に15vol%硫酸溶液を滴下後、ガラス板を重ねて、24時間放直後、表面の変化状態を観察することにより判断。
エポキシ系強化システム用途
従来よりスミカエクセル5003PSはエポキシ系強化システム用途に使用されてきました。5003PS使用のメリットは次のとおりです。
- エポキシの破壊強度を向上させます。
- 非常に高いTgを有します。
- 優れた機械的性質を有しています。
エポキシ樹脂の靭性強化
スミカエクセル5003PSは本質的に靭性があり、高いTgと弾性率を有しているので、システム全体の性能を低下させることなく、エポキシに靱性を付与することができます。下記表より大幅な破壊強度(GIC)の増加が見られ、Tgはそれほど低下していないことがわかります。
表7-6 TGDDM/4,4-DDS系での効果
5003PS濃度(%) | 曲げ弾性率(GPa) | Tg(℃) | GIC(kJ/m2) |
---|---|---|---|
0 | 3.34 | 205 | 0.28 |
10 | 3.21 | 205 | 0.41 |
15 | 3.07 | 200 | 0.47 |
(注)
1)GICは-65℃で平面歪み条件下で測定
2)Tgは捻れDMAで測定
エポキシレジン/As4CF系、ポリマー濃度30wt%での比較検討結果
表7-7 スミカエクセルPESとPEIの比較
評価項目 | 単位 | PEI | 5003PS | |
---|---|---|---|---|
CAI(Compressive After Impact strength) | MPa | 194 | 223 | |
圧縮強度 | (室温) | MPa | 1697 | 1731 |
(82℃) | 7434 | 1648 | ||
(82℃)/Wet | N/A | 1076 | ||
88℃粘度(Pa・s) | 130 | 100 |
N/A:分析データなし
航空機・スポーツ用品分野へのスミカエクセルPESの応用
CFRP(炭素繊維と樹脂とからなる複合材料)のマトリックス樹脂には熱硬化性エポキシ樹脂が使用されています。
エポキシ樹脂は機械的、熱的特性は優れていますが熱可塑性樹脂に比べると脆い欠点があります。航空機・スポーツ用品分野での利用においては破壊靱性(衝撃後圧縮強さ:CAI = Compressive After Impact strength)の向上が必須とされます。5003Pを添加することによりエポキシ樹脂と反応してマトリックス樹脂中の層間剥離を伴う衝撃破壊に対して高靱性を持たせることができます。
スミカエクセルPESの使用法
エポキシ主剤に5003Pを溶解し、均一系とします。これに硬化剤を加えて硬化させると5003Pの水酸基と反応して、海島構造の特殊なモルホロジーを形成して耐衝撃性が改善されます。エポキシ主剤に5003Pを溶解して均一系を得るには、5003Pを微粉砕して直接エポキシ主剤にN2雰囲気下、150℃程度で溶解させるか、溶媒にエポキシ主剤と5003Pを均一溶解させ、その後に溶媒を留去して均一系を得る方法があります。
単位コンポジット当たりのスミカエクセルPES使用量(例)
- 単位マトリックスレジン当たり
エポキシ主剤(100部):硬化剤(30~40部):5003P(30部) - 単位プリプレグ当たり
~10wt%
航空機用構造材としての使用法
実際に航空機等の構造材としての使用にあたっては、上記スミカエクセル5003Pの使用法で調製して得られるCFプリプレグの表面に、5003Pの粒度調整した粒子(Tough ball)をまぶして数十枚積層して成形すると、界面にあるPES ballによって耐衝撃性が更に向上します。
積層の方法については、種々な工夫がなされています。
(例:Boeingの航空機構造材としての規格)
- CAI(Compressive After Impact strength)値が310MPa以上
- CS(Compressive Strength.Hot/Wet Condition)値が1100MPa(82℃)以上
接着剤用途
スミカエクセルPESは耐熱接着剤として利用できます。特に、金属同士の接着では優れた接着強度を有します。
特徴
- 接着層は高い引張せん断接着強度と、T形剥離接着強度を有し、剛性と可撓性を併せもつバランスのとれた特性を示します。
- 市販熱可塑性樹脂接着剤の中では最高の耐熱性を有し、200℃においても実用的な引張破断接着強度は20MPaと非常に高いものです。
また、短時間であれば250℃までの温度でくり返し使用できます。 - 耐薬品性、耐熱性が優れています。
- 溶剤または揮発成分を含まず、アルミニウム、ステンレス、鋼、真ちゅう等の広範囲の材料に対してプライマーなしで優れた接着性を示します。
接着方法
スミカエクセルPESフィルム使用のホットメルトタイプ接着方法
- 被着体の大きさにフィルムを切断します。
- 必要に応じて被着体表面をサンドペーパー、ディスクサンダー等で粗面化し、アセトン、トルエン等で清浄します。
- 被着体の間にフィルムを挟み、治具を使用して軽く圧着して300~360℃で10~30分加熱します。圧着の程度は溶融した樹脂が被着体の間から僅かにバリとして出る程度で十分です。
- 放冷すれば強固な接着体が得られます。
接着溶液を用いる接着方法
スミカエクセル5003PSの溶媒系
5003PSを単一溶媒に溶解すると不安定でPESが析出するため、通常混合溶媒系を使用します。(単一溶媒では溶液安定性が低くゲル化します。)
表7-8 スミカエクセル5003PSの混合溶媒系の例
溶媒 | 溶媒 | 混合比(体積比) |
---|---|---|
A | ジメチルホルムアミド シクロヘキサノン メチルエチルケトン |
20 80 25 |
B | N-メチル-2-ピロリドン トルエンまたはキシレン |
2 1 |
C | N-メチル-2-ピロリドン トルエンまたはキシレン シリコン流動調節剤 メチルエチルケトン |
60 30 0.5~1 35 |
D | スルホラン γ-ブチロラクトン |
1 1 |
E | スルホラン アセトンまたはメチルエチルケトン |
1 1 |
接着方法
PES接着剤の接着強度は、熱処理条件によって変化するため、使用方法に応じた条件設定が必要です。
(条件例1)130℃、2時間乾燥
(条件例2)100℃、1時間後に350℃で15分間乾燥
スミカエクセル5003PS接着剤系の性質
高温下での接着強度に優れます。例として、18-8ステンレス同士をスミカエクセル5003PS接着剤系を使用して接着した場合、温度を220℃まで上昇させた時の接着強度の変化と150℃でエージングした場合の接着力保持率についての結果を表7-9と表7-10に示します。
表7-9 剥離強度と温度の影響
温度(℃) | 剥離強度(MPa) |
---|---|
23 | 37 |
150 | 26 |
220 | 14 |
剥離強度の測定は剥離速度12.5mm/minで行った。
表7-10 剥離強度と高温保持時間の影響
150℃での保持時間(hr) | 150℃での剥離強度(MPa) |
---|---|
0 | 26 |
1000 | 21 |
150℃、1000時間保持しても初期の接着強度の81%を保持している。
PESメンブランフィルター製カートリッジフィルター(ご提供:東洋濾紙株式会社)
PES製のメンブランフィルターとポリプロピレンから構成された、耐薬品性、耐熱性に優れたカートリッジフィルターです。
特徴
- 溶出する物質がほとんど無く、前処理としてのカートリッジ洗浄が少量で済みます。
- メディアが非対称であり、また、異孔径のプレメンブランフィルターを内蔵する為、高効率・高流量で長い濾過寿命が得られます。
- オートクレーブ滅菌、インラインスチーム減菌が行なえます。
- メディア自体が不活性であるため、試料中の成分が吸着されることはほとんどありません。
応用用途
- エレクトロニクスにおける超純水の精密濾過。
- プロセスガス、ベントエアーの除粒子、除菌濾過。
図7-2
