- Product Info
- SUMIKAEXCEL PES
- Chemical stability
Chemical stability of SUMIKAEXCEL PES
- SUMIKAEXCEL PES does not undergo hydrolysis.
- Be careful as it may be corroded by strong acids.
- Among amorphous polymers, SUMIKAEXCEL PES has excellent chemical resistance, but caution is required depending on the conditions of use. It is subject to stress cracking by certain organic chemicals, especially ketones and esters. In addition, it dissolves in highly polar solvents such as dimethyl sulfoxide (DMSO), aromatic amines, nitrobenzene, and certain chlorinated hydrocarbons (dichloromethane, chloroform, etc.).
- It has excellent resistance to aliphatic hydrocarbons, alcohols, some chlorinated hydrocarbons, some aromatic chemicals, oils, and greases, and is not affected by most bleaches and disinfectants when used under normal conditions.
- For practical use, evaluation of actual molded products is required.
Annealing
Residual stress in molded products can be relieved by annealing, which is effective in improving chemical resistance. This can be easily confirmed by immersing the product in toluene or methyl ethyl ketone (MEK).
Heat and water resistance
It does not undergo hydrolysis and can be used in hot water at 160℃ or in steam. However, care must be taken as the properties change due to water absorption.
Table 3-5-1 Resistance in hot water under load (hot water 90°C)
Stress (MPa) | ||||||
---|---|---|---|---|---|---|
13 | 20 | 26 | 33 | 40 | ||
SUMIKAEXCEL PES | 4100G | R56.5 | R20.2 | R15.3 | R12.5 | - |
4800G | 989.6 | R65.5 | R18.7 | - | - | |
4101GL30 (GF30%) | - | - | 987.3 | 732.5 | R25.5 | |
PPS (GF40%) | - | - | R130 | R87 | - |
In the table [R=Ruptured, numbers indicate elapsed time]
For 4100G, cracks occurred in 56.5 hours under a load of 13 MPa.
4101GL30: No problems for up to 987.3 hours under a load of 26 MPa
(This does not mean that cracks will occur in 987.3 hours).
Table 3-5-2 Hot water resistance at 140℃ (4100G)
Duration (weeks) | Tensile strength (MPa) | Percentage change | Charpy impact strength (kJ/m2) | Percentage change |
---|---|---|---|---|
Control | 81 | 100 | 39 | 100 |
2 | 88 | 108 | 18 | 46 |
7 | 93 | 114 | 14 | 35 |
14 | 92 | 113 | 14 | 34 |
29 | 81 | 100 | 14 | 37 |
42 | 84 | 104 | 15 | 39 |
- Steam sterilization at 140℃
Even if SUMIKAEXCEL PES is steam sterilized at 140℃ for 24 hours, there is no change in the tensile strength.
*4800G, which has a higher molecular weight than 4100G, can withstand harsh hot water conditions.
Chemical resistance
It is resistant to oils such as gasoline and engine oil, greases, and cleaning solvents such as chlorocene and freon. However, it is corroded by polar solvents such as acetone and chloroform, so care must be taken when using them. On the other hand, its stress cracking resistance is the best among amorphous polymers. It is also resistant to alkalis and acids even at high temperatures.
Table 3-5-3 Chemical resistance and stress cracking resistance
Immersion Test | Stress cracking resistance test | ||
---|---|---|---|
4800G | 4800G | Polysulfone | |
Ammonia | A | - | - |
50% caustic soda | A | - | - |
Concentrated hydrochloric acid | A | - | - |
10% Nitric Acid | A | - | - |
Concentrated Nitric Acid | C | - | - |
Hydrogen peroxide | A | - | - |
Benzene | A | a | c |
Xylene | B | a | c |
Acetone | C | c | c |
Methyl Ethyl Ketone | C | c | c |
Heptane | A | a | a |
Cyclohexane | A | a | a |
Glycerin | A | a | a |
Ethylene glycol | A | a | a |
Carbon tetrachloride | A | a | a |
Gasoline | A | a | b |
Ethyl acetate | C | b | c |
A: No impact.
B: There is some impact.
C: Not fit for use.
a: It can be used except when the load is extremely heavy.
b: May only be used for light loads.
c: Not fit for use.
Table 3-5-4 Changes in weight and tensile strength when immersed in inorganic chemicals
Chemical Name | Grade | Temperature (℃) | Weight change | Tensile strength change (%) | remarks | |||||
---|---|---|---|---|---|---|---|---|---|---|
Immersion time | Weight change | Immersion time (days) | ||||||||
(days) | (%) | 14 | 30 | 90 | 180 | 360 | ||||
Water | 4100G | room temperature | 1 | 0.43 | - | -17.7 | -16.6 | -21.1 | - | - |
Water | 4100G | 50 | - | - | - | -13.5 | -13.1 | -17.7 | - | - |
Water | 4100G | 100 | - | - | 7.0 | 7.4 | 9.8 | 9.2 | 9.5 | - |
10% hydrochloric acid | 4100G | room temperature | 180 | 1.95 | -15.6 | -14.9 | -17.8 | -21.1 | - | - |
Concentrated hydrochloric acid | 4100G | room temperature | 180 | 2.19 | - | -6.3 | -12.2 | -21.1 | - | - |
15% hydrochloric acid | 4100G | 90 | - | - | - | - | -40.0 | -49.0 | -53.0 | Quite a lot of crazes |
10% sulfuric acid | 4100G | room temperature | 180 | 1.82 | - | -13.2 | -17.7 | -23.4 | - | - |
50% sulfuric acid | 4100G | 60 | 14 | -0.39 | 6.3 | - | - | - | - | - |
50% sulfuric acid | 4101GL30 | 60 | 14 | -0.20 | - | - | - | - | - | - |
Concentrated sulfuric acid | 4100G | room temperature | - | - | - | - | - | - | - | Dissolution |
25% sulfuric acid | 4100G | 90 | - | - | - | - | 2.0 | 3.0 | 7.0 | - |
40% sulfuric acid | 4100G | 60 | 14 | -0.55 | - | - | - | - | - | - |
40% phosphoric acid | ||||||||||
40% sulfuric acid | 4101GL30 | 60 | 14 | -0.37 | - | - | - | - | - | - |
40% phosphoric acid | ||||||||||
10% sulfuric acid | 4100G | room temperature | 180 | 2.27 | - | - | - | - | - | - |
Concentrated Nitric Acid | 4100G | room temperature | - | - | - | - | - | - | - | Dissolution |
5% nitric acid | 4100G | 90 | - | - | - | - | 0.0 | -29.0 | -24.0 | Slightly crazed |
10% caustic soda | 4100G | room temperature | 180 | 1.79 | - | -13.9 | -18.2 | -22.3 | - | - |
Saturated Caustic Soda | 4100G | room temperature | 180 | 0.82 | - | -4.8 | -11.0 | -14.2 | - | - |
5% caustic soda | 4100G | 90 | - | - | - | - | 3.0 | 2.0 | 6.1 | - |
Saturated potassium chloride | 4100G | room temperature | 120 | 1.46 | - | - | - | - | - | - |
Saturated sodium hypochlorite | 4100G | room temperature | 180 | 1.42 | - | -9.8 | -15.8 | -19.6 | - | - |
25% saturated sodium hypochlorite | 4100G | 90 | - | - | - | -10.0 | -9.0 | -6.0 | - | - |
10% ammonium hydroxide | 4100G | room temperature | 120 | 1.63 | - | - | - | - | - | - |
Hydrogen peroxide | 4100G | room temperature | 120 | 2.52 | - | -9.8 | - | - | - | - |
Chlorinated bromine water (PH4) | 4100G | 90 | 30 | 0.33 | - | -1.0 | - | - | - | - |
5% Alum | 4100G | 90 | - | - | - | - | -8.0 | -11.0 | -12.0 | Slightly crazed |
Sulfur dioxide gas | 4100G | room temperature | 180 | 8.49 | - | -15.0 | - | -34.0 | - | - |
Nitrogen dioxide | 4100G | room temperature | 180 | 1.19 | - | -4.5 | - | -4.5 | - | - |
Sulfur hexafluoride | 4100G | room temperature | 30 | -0.11 | - | 2.4 | - | - | - | - |
Chlorine | 4100G | room temperature | 28 | 0.47 | - | -62.8 | - | - | - | Cracks occur |
Resistant to organic chemicals
Stress cracking resistance
A constant load is applied to a tensile impact test piece (1.6 mm thick), and the condition of the test piece after immersion in each chemical for up to 20 minutes is shown according to the legend.
Table 3-5-5 Stress cracking resistance
Stress 10MPa | Stress 19MPa | |||||||||||
---|---|---|---|---|---|---|---|---|---|---|---|---|
Polyethersulfone | Poly Sulfone |
Poly Carbonate |
Modified PPO |
Polyethersulfone | Poly Sulfone |
Poly Carbonate |
Modified PPO |
|||||
4100G | 4800G | 4101GL30 | Non-reinforced | Non-reinforced | Non-reinforced | 4100G | 4800G | 4101GL30 | Non-reinforced | Non-reinforced | Non-reinforced | |
Acetone | R1S | R4S | ○ | R2S | R1S | ○ | R1S | R3S | ○ | R2S | R1S | ○ |
Methyl Ethyl Ketone | R1S | R2S | ○ | R1S | ○ | R18 | R1S | R1S | ○ | R1S | R5 | R20S |
Cyclohexanone | R1S | R19S | ○ | ○ | ○ | D | R1S | R5S | ○ | D | D | D |
Benzene | C20 | ○ | ○ | R1S | R4 | D | R2 | C20 | ○ | R1S | R3 | D |
Toluene | ○ | ○ | ○ | R1S | R11 | D | R6 | C20 | ○ | R1S | R3 | D |
Xylene | ○ | ○ | ○ | R4S | R15 | D | ○ | ○ | ○ | R2S | R11 | D |
Trichloroethylene | C20 | C20 | ○ | D | ○ | D | R6 | R11 | ○ | D | R17 | D |
1.1.1-Trichloroethane (Chlorocene) |
○ | ○ | ○ | R8S | R3 | D | ○ | ○ | ○ | R3S | R1 | D |
Carbon tetrachloride | ○ | ○ | ○ | SLC20 | R6S | D | ○ | ○ | ○ | R3 | R3S | D |
1.2-Dichloroethane | R1S | R1S | ○ | D | D | D | R1S | R1S | ○ | D | D | D |
Perchloroethylene | ○ | ○ | ○ | C20 | R1S | D | ○ | ○ | ○ | R8 | R1S | D |
Chloroform | R1S | R1S | ○ | D | D | D | R1S | R1S | ○ | D | D | D |
Trichlorotrifluoroethane (Freon) |
○ | ○ | ○ | ○ | ○ | D | ○ | ○ | ○ | ○ | ○ | D |
Methanol | ○ | ○ | ○ | ○ | ○ | ○ | ○ | ○ | ○ | ○ | ○ | ○ |
Ethanol | ○ | ○ | ○ | ○ | ○ | ○ | ○ | ○ | ○ | ○ | ○ | ○ |
n-Butanol | ○ | ○ | ○ | ○ | ○ | ○ | ○ | ○ | ○ | C20 | C20 | ○ |
Ethylene glycol | ○ | ○ | ○ | ○ | ○ | ○ | ○ | ○ | ○ | ○ | ○ | ○ |
2-Ethoxyethanol | C20 | SLC20 | ○ | C20 | R17 | ○ | C20 | C20 | ○ | C20 | R10 | ○ |
Propane-1,2-diol | ○ | ○ | ○ | ○ | ○ | ○ | ○ | ○ | ○ | ○ | ○ | ○ |
Heptane | ○ | ○ | ○ | ○ | ○ | ○ | ○ | ○ | ○ | ○ | SLC20 | R19 |
Ethyl acetate | R315 | C20 | ○ | R3S | ○ | ○ | R17S | R7 | ○ | R1S | R4 | ○ |
Diethyl Ether | C20 | S1.C20 | ○ | C20 | R1 | ○ | C20 | C20 | ○ | R7 | R1 | R15 |
Carbon dioxide | ○ | ○ | ○ | R8S | R1S | D | ○ | ○ | ○ | R5S | R1S | D |
Gasoline | ○ | ○ | ○ | ○ | C20 | ○ | ○ | ○ | ○ | C20 | R3 | R1 |
Light oil | ○ | ○ | ○ | ○ | ○ | ○ | ○ | ○ | ○ | ○ | ○ | ○ |
(Legend) | ○ | ...The test piece showed no change even after 20 minutes of immersion. | R8 | ...After 8 minutes of immersion it cracked. |
C20 | ...After 20 minutes of immersion, crazing occurred. | R2S | ...After 2 seconds of immersion it broke. | |
SLC20 | ...After 20 minutes of immersion, slight crazing occurred. | D | ...The test piece dissolved. |
Solubility
SUMIKAEXCEL PES is a polar polymer, so it dissolves in polar solvents. The solubility of SUMIKAEXCEL PES is important for paint and coating applications and solvent adhesion. Solvents for SUMIKAEXCEL PES include dimethyl sulfoxide, N-dimethylformamide, N-methylpyrrolidone, and dimethylacetamide.
Weight and tensile strength changes due to organic chemicals
Table 3-5-6 shows the weight change when immersed in various organic chemicals. For non-solvents, the weight changes by -0.5 to 2% depending on the immersion temperature and time, but the dimensions do not change. For some solvents, the material generally softens, swells, and its weight increases significantly.
Table 3-5-6 Changes in weight and tensile strength when immersed in organic chemicals
Product name | Grade | temperature (℃) |
Weight change | Tensile strength change | remarks | |||||
---|---|---|---|---|---|---|---|---|---|---|
Immersion time (days) |
Weight change (%) |
Immersion time (days) | ||||||||
7 | 30 | 90 | 180 | 360 | ||||||
25% acetic acid | 4100G | 90 | - | - | - | - | -3.00 | -27.00 | -42.00 | Craze occurs in 360 days |
Glacial Acetic Acid | room temperature | 30 | 0.31 | - | - | - | - | - | - | |
5% phenol | room temperature | 90 | 6.66 | -29.70 | -35.70 | -45.80 | - | - | - | |
Anhydrous Hydrazine | room temperature | 14 | 3.50 | - | - | - | - | - | softening | |
Benzene | room temperature | 180 | 1.48 | -3.20 | -3.10 | -8.60 | -13.50 | - | - | |
Xylene | room temperature | 7 | 0.49 | - | - | - | - | - | - | |
Heptane | room temperature | 180 | 0.21 | -0.80 | -1.00 | -5.80 | -10.00 | - | - | |
Cyclohexane | room temperature | 120 | 0.12 | - | - | - | - | - | - | |
Methanol | room temperature | 14 | 2.09 | - | - | - | - | - | - | |
Ethanol | room temperature | 180 | 1.46 | -2.20 | -5.00 | -13.60 | -18.70 | - | - | |
Ethylene glycol | room temperature | 120 | 0.53 | - | - | - | - | - | - | |
Propylene Glycol | 100 | 14 | -0.36 | - | - | - | - | - | - | |
Glycerin | 150 | 14 | 0.06 | - | - | - | - | - | - | |
White Spirit | 130 | 7 | -0.51 | +21.90 | - | - | - | - | Slightly cracked | |
Ethyl acetate | room temperature | 60 | 10.70 | - | - | - | - | - | softening | |
Amyl Acetate | room temperature | 120 | -0.08 | - | - | - | - | - | - | |
Diethyl Ether | room temperature | 120 | 2.91 | - | - | - | - | - | - | |
Carbon tetrachloride | room temperature | 180 | 0.44 | -0.40 | -0.30 | -6.40 | -11.30 | - | - | |
1.1.1-Trichloroethane (Chlorocene) |
room temperature | 120 | 1.01 | -10.20 | -19.20 | -32.80 | -51.60 | - | - | |
Genkleine | room temperature | 120 | 1.13 | - | - | - | - | - | - | |
Parkren | room temperature | 120 | 0.78 | - | - | - | - | - | - | |
North Sea Gas | room temperature | 180 | 0.01 | - | -0.34 | - | 0.20 | - | - | |
Ethylene oxide | room temperature | 190 | 7.59 | - | -14.00 | - | -39.10 | - | Cracks occur under a stress of 140kg/ cm2 | |
Propylene Gas | room temperature | 180 | 0.21 | - | - | - | -0.11 | - | - |
Cleaning Solvent
It is often necessary to remove grease, oil, and release agents from the surface of molded products, especially when painting or gluing. In this case, avoid using cleaning solvents such as acetone and methyl ethyl ketone. The following table shows the effect of cleaning solvents on 4100G.
Table 3-5-7 Effects of cleaning solvents (4100G)
Washing solvent (reflux) | Minutes | Hardness (initial value = 98) | Weight gain (%) |
---|---|---|---|
Arklone P | 2 | 98 | 0 |
10 | 98 | 0 | |
30 | 98 | 0 | |
Arklone L | 2 | 98 | 0 |
10 | 98 | 0 | |
30 | 98 | 0 | |
Genkleine | 2 | 98 | 0 |
10 | 98 | 0 | |
30 | 98 | 0 | |
Trinklone A | 2 | 98 | 0 |
10 | 98 | 1 | |
30 | 98 | 1 | |
Trinklone N | 2 | 98 | 1 |
10 | Cracks appear on the surface | 1 | |
30 | Cracks appear on the surface | 2 | |
Perchloroethylene | 2 | 98 | 0 |
10 | 98 | 0 | |
30 | 98 | 0 | |
Methylene chloride | 2 | 98 | 3 |
10 | Dissolution | ||
30 | Dissolution |
Resistant to oil, gasoline and transmission oil
Table 3-5-8 Weight change in oil and gasoline (4100G)
Environment | Immersion time (days) | Temperature (℃) | Weight change (%) |
---|---|---|---|
Linseed oil | 180 | room temperature | 0.63 |
Deep Frying Oil | 2 | 180 | -0.10 |
Silicone oil (ICI 190) | 180 | room temperature | 0.37 |
Veedol ATF 3433 (transmission oil) | 365 | 130 | 0.38 |
Castrol ATF | 90 | 160 | -0.55 |
Shell Diala Transformer Oil | 180 | room temperature | 0.30 |
Castrol ATF Solvent flushing oil | 90 | room temperature | 0.50 |
Duckhamz 20/50 oil | 90 | 160 | 2.84 |
Gunk | 90 | room temperature | 0.55 |
98 octane gasoline | 180 | room temperature | 0.60 |
3 Star Petrol | 90 | room temperature | 0.20 |
ASTM II Oil | 7 | room temperature | 0 |
Figure 3-5-1 Changes in mechanical properties in transmission oil (4100G)
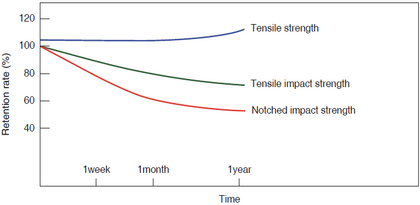
(Immersion conditions)
Transmission oil VEEDOL ATF
Temperature: 130℃
Table 3-5-9 Stress cracking resistance in gasoline (room temperature)
Grade | Environment | Stress (MPa) | |||
---|---|---|---|---|---|
9 | 19 | 28 | 37 | ||
4100G | Diesel Gasoline | 20 | 20 | 20 | 20 |
4100G | 97 octane gasoline | 20 | 20 | SLC20 | C20 |
4100G | 100 octane gasoline | 20 | R270h | C20 | R19 |
4100G | paraffin | 2110h | 2110h | 2110h | 2110h |
4101GL30 | 97 octane gasoline | 20 | 20 | 20 | 20 |
4101GL30 | 100 octane gasoline | 360h | 360h | 20 | 20 |
R | :crack |
C | : Crazing occurs |
SLC | : Slight crazes |
h | : Time If there is no unit, it is minutes. |
(Legend) | 20 | : No problem for 20 minutes |
R270h | Cracks appear after 270 hours | |
2110h | :21 No problem up to 10 hours |
Table 3-5-10 Stress cracking resistance in oil (Vactralite Oil) (100℃)
Grade | Notch Radius (mm) |
Stress (MPa) | |||||
---|---|---|---|---|---|---|---|
5 | 10 | 20 | 25 | 30 | 40 | ||
4100G | 0.01 | 2000h | R150h | - | - | - | - |
4100G | 0.25 | 2300h | R110h | - | - | - | - |
4100G | 0.50 | - | 1450h | R330h | - | - | - |
4100G | 1.00 | - | 2000h | 2000h | - | 3000h | R790h |
4100G | 2.50* | - | - | 2300h | - | 2000h | R700h |
4101GL20 | 0.50 | - | - | - | 1632h | R460h | R160h |
*Mold notch
(Items without an * are machine notches)
(Legend) | 20 | : No problem for 20 minutes |
R270h | Cracks appear after 270 hours | |
2110h | :21 No problem up to 10 hours |
Table 3-5-11 Stress cracking resistance in turbine oil (160℃)
Grade | oil | Notch Radius (mm) |
Stress (MPa) | |||
---|---|---|---|---|---|---|
10 | 20 | 30 | 40 | |||
4800G | Aeroshell 555 | 2.5 | 3000h | R1h | - | - |
4101GL20 | Aeroshell 555 | 0.5* | 250h | R3h | - | - |
4101GL30 | Aeroshell 555 | 2.5 | - | 3700h | - | - |
4800G | Esso Turbo 2380 | 2.5 | 3200h | - | - | - |
4101GL30 | Esso Turbo 2380 | 2.5 | - | - | 1650h | R2h |
4800G | Esso Turbo 2389 | 2.5 | 1400h | R20h | - | - |
*Mold notch
(Items without an * are machine notches)
(Legend) | 20 | : No problem for 20 minutes |
R270h | Cracks appear after 270 hours | |
2110h | :21 No problem up to 10 hours |
Table 3-5-12 Effect of oil on mechanical properties (4800G)
Oil Type | Temperature (℃) | Immersion time (weeks) | ||||||
---|---|---|---|---|---|---|---|---|
2 | 4 | 6 | 16 | 32 | 52 | |||
Mineral oil | 100 | + | + | + | + | + | + | |
120 | + | + | + | + | 0 | 0 | ||
140 | + | 0 | 0 | 0 | 0 | |||
Synthetic Hydrocarbon Oil | 100 | + | + | + | + | 0 | 0 | |
120 | + | + | + | + | 0 | 0 | ||
140 | 0 | 0 | 0 | 0 | - | |||
Silken Oil | Dimethyl | 120 | + | + | + | + | 0 | 0 |
160 | + | 0 | 0 | 0 | 0 | 0 | ||
Methylphenyl | 120 | + | + | + | + | + | + | |
140 | + | + | + | 0 | 0 | |||
160 | + | 0 | 0 | 0 | 0 | 0 | ||
180 | + | 0 | - | - | - | - | ||
Chlorophenyl | 160 | 0 | 0 | 0 | 0 | 0 | 0 | |
180 | - | - | - | - | - | - | ||
200 | - | - | - | - | - | - | ||
Ester Oil | Diester | 120 | + | + | + | + | 0 | 0 |
polyester | 120 | + | + | 0 | 0 | - | - | |
160 | 0 | 0 | - | - | - | - | ||
180 | 0 | - | - | - | - | - | ||
Polyglycol Oil | 100 | + | + | + | + | + | + | |
120 | + | + | + | 0 | 0 | 0 | ||
140 | 0 | 0 | 0 | 0 | 0 | |||
Fluorinated alkyl ether oil | 180 | 0 | 0 | 0 | - | - | - | |
200 | - | - | - | - | - | - | ||
Water-based oil emulsion | 80 | 0 | 0 | 0 | 0 | - | - | |
Mineral base oil +Thickener |
a) Calcium soap | 80 | + | + | 0 | 0 | 0 | 0 |
b) Lithium soap | 120 | + | 0 | 0 | - | - | - | |
c) Lithium lead soap | 120 | 0 | 0 | 0 | 0 | - | - | |
d) Calcium complex soap | 120 | + | + | + | + | + | - | |
e) Sodium synthetic soap | 120 | 0 | 0 | 0 | - | - | - | |
f) Polyurea | 120 | 0 | 0 | 0 | 0 | - | - | |
Diester + Lithium Soap | 120 | + | + | + | + | 0 | 0 | |
Silicone-based oil | Dimethyl + modified amide | 120 | + | 0 | 0 | 0 | 0 | 0 |
Methylphenyl + Lithium Soap | 120 | + | + | + | + | 0 | 0 | |
140 | + | + | + | + | ||||
160 | + | + | 0 | 0 |
Usage Guide | Resistance | Retention Rate |
+ | Excellent | Over 75% |
0 | good | More than 50% |
- | No | Less than 50% |
Table 3-5-13 Stress cracking resistance when subjected to a certain deformation in various turbine oils (4800G)
oil | Temperature | |||
---|---|---|---|---|
room temperature | 150℃ | 160℃ | ||
Deformation amount | ||||
3% | 2% | 1% | 0% | |
Aeroshell 500 | 0.05 | R5 | 0.15 | 15 |
Aeroshell 555 | 5 | R5 | 15* | 15 |
Aeroshell 750 | 5 | R5 | 15 | - |
Castrol 580 | 5 | R5 | 15 | - |
Esso Turbo 25 | 5 | R5 | 25 | - |
Esso Turbo 274 | 5 | R5 | R25 ** | 15 |
Esso Turbo 2380 | 5 | R5 | R25 ** | 15 |
Esso Turbo 2389 | 5 | R5 | - | - |
20: No problems for 20 minutes | ||
(Legend) | * | The surface cracks are parallel to the resin flow direction. |
** | No cracks occurred in 25 minutes. |
Resistant to bleach and sterilizing fluids
SUMIKAEXCEL PES is only slightly affected by most bleaches and sterilizing solutions unless they are highly concentrated. After immersion in a sterilizing solution, if SUMIKAEXCEL PES molded product is to be subsequently sterilized by steam or dry heat, it must be thoroughly washed with water.
Table 3-5-14 Effects of bleach and sterilizing fluids (4100G)
solution | Weight change (%) | Tensile strength change (%) |
---|---|---|
10% Lissapol N | 1.46 | -11.6 |
2% lvisol | 1.35 | -14.6 |
0.5% Gevisol | 1.40 | -14.8 |
2% Instrument | 1.42 | -15.6 |
1% Bentenol | 1.30 | -13.6 |
1% Soillay 901-SD | 1.36 | -14.7 |
Household bleach | 1.27 | - |
Immersion conditions: Room temperature for 1 month