- Product Info
- SUMIKAEXCEL ™ PES
- Injection molding conditions
Injection molding conditions for SUMIKAEXCEL PES and SUMIPLOY
Molding conditions
The standard molding conditions for SUMIKAEXCEL PES and SUMIPLOY are shown below.
Table 4-1-1 Standard molding conditions for SUMIKAEXCEL PES
Grade | 3600G 4100G |
4800G | 3601GL20 / 3601GL30 4101GL20 / 4101GL30 ES5340 |
||||
---|---|---|---|---|---|---|---|
Recommended conditions | Condition Range | Recommended conditions | Condition Range | Recommended conditions | Condition Range | ||
Drying temperature (℃) | 160~180 | 160~180 | 160~180 | ||||
Drying time (hr) | 5~24 | 5~24 | 5~24 | ||||
Cylinder temperature (℃) | Rear end | 320 | 300~340 | 320 | 320~340 | 320 | 300~340 |
Center | 340 | 320~370 | 340 | 330~370 | 340 | 320~370 | |
Front | 350 | 330~380 | 360 | 340~390 | 350 | 330~380 | |
Nozzle | 350 | 330~380 | 360 | 340~390 | 350 | 330~380 | |
Optimum resin temperature (℃) | 350 | 350~360 | 360 | 350~370 | 350 | 350~360 | |
Mold temperature (℃) | 140~180 | 120~180 | 140~180 | 120~180 | 140~180 | 120~180 | |
Injection pressure (MPa) | 100~200 | 100~200 | 100~200 | 100~200 | 100~200 | 100~200 | |
Injection Speed | Slow | Low to medium speed | Slow | Low to medium speed | Slow | Low to medium speed | |
Screw rotation speed (rpm) | 50~100 | 50~100 | 50~100 | 50~100 | 50~100 | 50~100 | |
Screw back pressure (MPa) | 5~10 | 5~10 | 5~10 | 5~20 | 5~10 | 5~10 | |
Holding pressure (MPa) | 50~100 | 50~100 | 50~100 | 50~150 | 50~100 | 50~100 |
Table 4-1-2 Standard molding conditions for SUMIPLOY
Grade | GS5620 CS5220 / CS5530 / CS5600 |
E3010 FS2200 |
CK3400 / CK3420 CK4600 |
||||
---|---|---|---|---|---|---|---|
Recommended conditions | Condition Range | Recommended conditions | Condition Range | Recommended conditions | Condition Range | ||
Drying temperature (℃) | 160 | 160~180 | 160 | 160~180 | 160 | 160~180 | |
Drying time (hr) | 8 | 5~24 | 8 | 5~24 | 5 | 5~24 | |
Cylinder temperature (℃) | Rear end | 320 | 320~340 | 320 | 300~340 | 380 | 360~400 |
Center | 340 | 330~370 | 340 | 320~370 | 390 | 370~410 | |
Front | 360 | 340~390 | 350 | 330~380 | 390 | 380~420 | |
Nozzle | 360 | 340~390 | 350 | 330~380 | 400 | 380~420 | |
Optimum resin temperature (℃) | 360 | 340~390 | 350 | 350~360 | 400 | 380~420 | |
Mold temperature (℃) | 140~180 | 120~180 | 140~180 | 120~180 | 180 | 120~180 | |
Injection pressure (MPa) | 100~200 | 100~200 | 100~200 | 100~200 | 100~200 | 100~200 | |
Injection Speed | Slow | Low to medium speed | Slow | Low to medium speed | Slow | Low to medium speed | |
Screw rotation speed (rpm) | 50~100 | 50~100 | 50~100 | 50~100 | 50~100 | 50~100 | |
Screw back pressure (MPa) | 5~10 | 5~10 | 5~10 | 5~10 | 5~10 | 5~10 | |
Holding pressure (MPa) | 100~200 | 50~200 | 50~100 | 50~150 | 100~200 | 50~200 |
Pre-drying
SUMIKAEXCEL PES is absorbent, so it must be dried thoroughly. Use a hot air circulation oven or dehumidifying dryer to dry at 160-180°C for 5-24 hours. If using a shelf oven, spread the material out to a thickness of 50 mm or less before drying. Drying at 180°C is recommended, especially when molding large products.
In addition, for non-reinforced products and large moldings, we recommend using a dehumidifying dryer. If a hopper dryer is used, it must have a sufficient capacity and a large heat capacity. If pre-drying is insufficient, silver streaks, flash marks, etc. may appear on the surface of the molded product.
If any of the above occurs, further drying is required.
SUMIKAEXCEL PES does not hydrolyze, so it will not deteriorate when dried under the above conditions.
Figure 4-1-1 Drying curve of 4100G
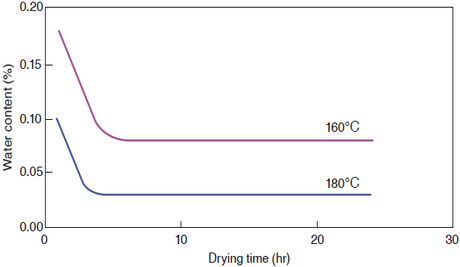
Resin Temperature
We recommend a resin temperature of 330 to 380°C. Because SUMIKAEXCEL PES has a high melt viscosity, the resin temperature tends to be higher than the cylinder temperature setting due to shear heating, and there may be a difference of 40°C or more. It is necessary to check the resin temperature while molding.
Figure 4-1-2 Flow length of PES (1mm)
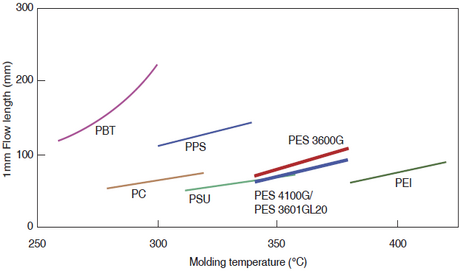
Resin residence time
The length of time the material stays in the cylinder has a significant effect on the quality of the injection molded product. The residence time should be kept to 10 minutes or less. If the residence time is longer, there is a high possibility of thermal degradation, which may result in discoloration, black streaks, or black spots on the molded parts.
Mold Temperature
Set the mold temperature so that the surface temperature is 120 to 180°C. Also, design the mold so that the temperature distribution on the surface is small.
If the mold temperature is too low, residual stress will cause the molded product to warp or crack. In glass fiber reinforced grades, this can cause the glass fibers to protrude. By setting the mold temperature high, molded products with less residual stress can be obtained. However, if the mold temperature is too high, it can cause deformation when the molded product is removed.
Either the heater method or the oil temperature control method can be used as the heating method, but for molds with complex shapes, deep molds, or molds with slide cores, use the oil temperature control method and minimize the temperature distribution in the mold.
Particularly when molding large items or when using unreinforced parts, it is necessary to pay close attention to the mold temperature.
Injection pressure, holding pressure
Generally, high injection pressure is required for molding SUMIKAEXCEL PES, with an injection pressure of 100 to 200 MPa being necessary. Thin-walled molded products, glass fiber reinforced grades, and molded products with long flow lengths require an injection pressure of 150 MPa or more.
We recommend setting the holding pressure to 1/2 to 1/3 of the injection pressure. Set the holding pressure low enough to prevent sink marks. Lower holding pressure will result in molded products with less residual stress.
The higher the peak pressure or holding pressure, the more difficult it tends to be to release the mold, so adjust the VP switch position to prevent the peak pressure from rising too high.
Injection Speed
SUMIKAEXCEL PES is generally suitable for low to medium injection speeds, but the optimum injection speed varies depending on the shape of the molded product.
Since SUMIKAEXCEL PES has a high melt viscosity, if the injection speed is too fast, it may cause discoloration or silvering due to shear heating or adiabatic compression of the air.
On the other hand, thin-walled molded products (1 mm or less) and products with long flow distances require a high injection speed. Generally, a slower injection speed results in molded products with less residual stress.
Screw speed, back pressure
To prevent the resin temperature from rising due to shear heat, a slow screw rotation speed is preferable; we recommend 50 to 100 rpm.
Applying an appropriate back pressure will result in a uniform melted state. A back pressure of 5 to 10 MPa is preferable, and for grades with high molecular weights, a higher back pressure should be set. However, if the back pressure is too high, problems such as resin overheating and overloading may occur.
Temporary stop of molding
When temporarily suspending molding, set the cylinder temperature to 250-260°C to prevent thermal degradation of the resin. If the resin temperature falls below 250°C, it may damage the screw surface or the cylinder inner wall, or cause foreign matter to be generated when molding is resumed. If suspending molding for an extended period of time, purge the inside of the cylinder with purging material before lowering the cylinder temperature.
Purging Method
We will explain how to purge when using SUMIKAEXCEL PES.
Suitable purging materials are high molecular weight polyethylene or polycarbonate with an MFR of about 0.05, or glass fiber reinforced grades of these materials.
- Please be aware that due to the high processing temperatures, smoke, gas emissions, and resin scattering may occur.
- Be careful not to let the purging material remain inside the cylinder.
Table 4-1-3 Switching to SUMIKAEXCEL PES
Item | Recommended conditions | |
---|---|---|
Setting | Back pressure | High (enough so that the screw retracts slowly.) |
Screw Rotation Speed | Use the same rotation speed as when molding the preceding resin. | |
Washing Procedure | 1. Discharge of the preceding resin | Discharge as much of the resin from the hopper and cylinder as possible. |
2. Purging material injection and purging method | While the preceding resin is still at its molding temperature, add the purging material and purge thoroughly. Polycarbonate or high molecular weight polyethylene is suitable for the purging material. If you use a glass fiber reinforced purging material to improve the cleaning effect, please replace it with a non-filler purging material and then replace it with PES. Be careful not to leave any glass fibers behind. |
|
3. Temperature change | While running the purging material, change the temperature to the PES molding temperature. | |
4. Discharge of purging material and introduction of PES | When the molding temperature of PES is reached, thoroughly discharge the purging material and then add PES to purge. | |
5. Molding | After purging with PES, the cylinder temperature is stabilized and the material can be molded. |
Checking residual stress
Residual SUMIKAEXCEL in molded products can cause defects such as breakage or cracks when released from the mold. Adjust the holding pressure and holding time to achieve optimal conditions to prevent sink marks or overfilling.
The following method can be used to check the residual distortion of SUMIKAEXCEL PES injection molded products. This method can also be used to determine the optimal molding conditions.
- Test Method
- The part is allowed to cool to room temperature.
- The molded part is immersed in xylene for 90 seconds.
- Wash in cold water.
- Check carefully for cracks in the molded product.
- If no cracks are found, perform the same test in toluene, then change the solvent to ethyl acetate and then methyl ethyl ketone, in that order.
- If cracks occur, test several molded pieces using the solvent to confirm.
Table 4-1-4 How to check residual stress in SUMIKAEXCEL PES (4100G)
solvent | Residual distortion | Residual stress |
---|---|---|
Cracks occur with xylene | 1.3-1.5% or more | 30 to 40 MPa or more |
Cracks occur with toluene | 1.0% or more | Over 27MPa |
Cracks occur with ethyl acetate | 0.50% or more | 14MPa or more |
Cracks occur with methyl ethyl ketone | 0.35% or more | 10MPa or more |